Other Applications
DSG Technology In Robotic Applications
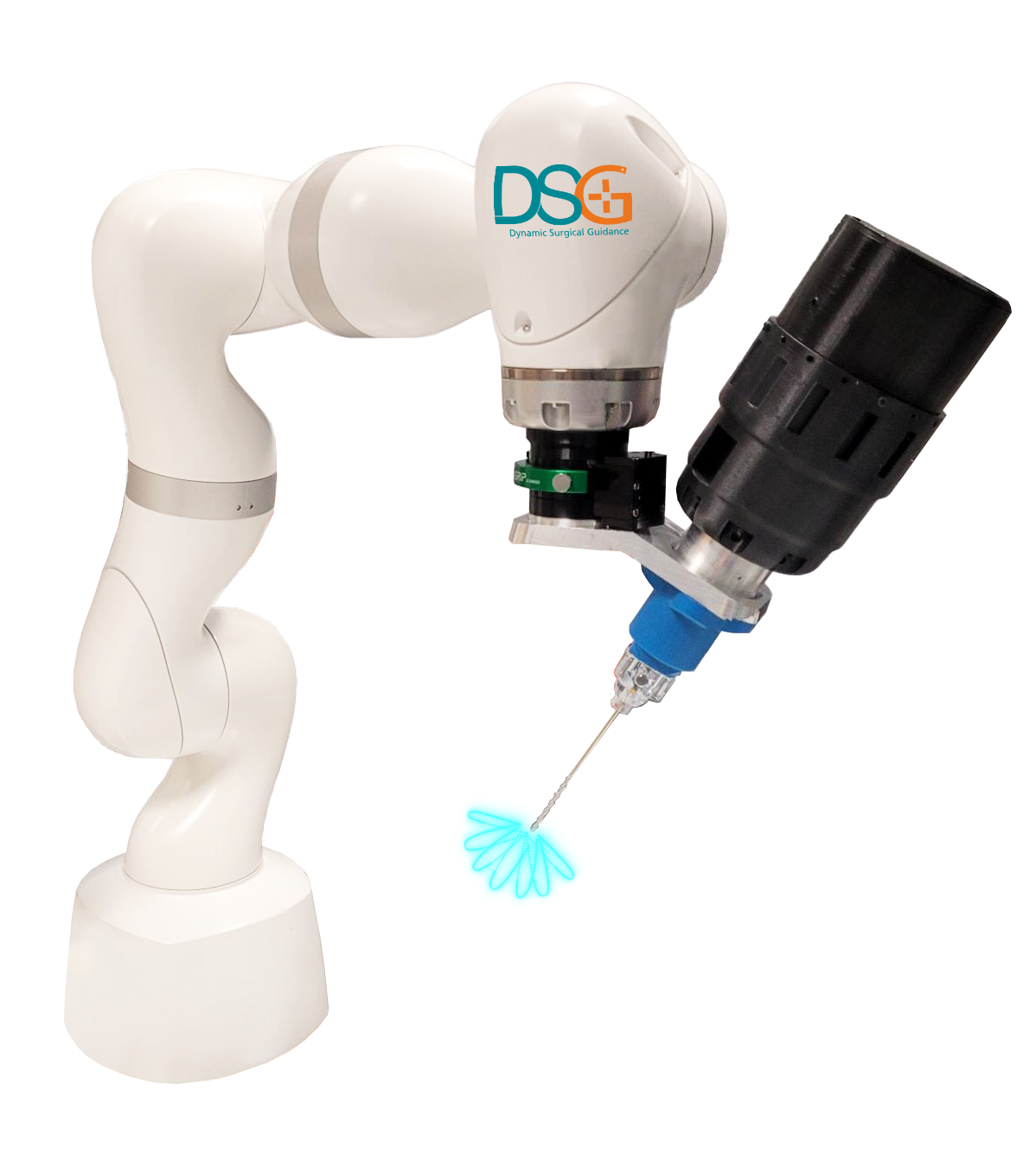
Main features
SpineGuard signed a partnership agreement with ISIR (Institut des Systèmes Intelligents et de Robotique), a laboratory affiliated to Sorbonne University, CNRS (Centre National de la Recherche Scientifique) and INSERM (Institut National de la Santé et de la Recherche Médicale), all specialized in surgical robotics. The objective is to scientifically prove that a robot combined with the DSG® technology can assure real time detection of breaches during surgical skeletal drillings, and make the implant placement possible with a robot autonomously.
This partnership has already demonstrated successful results with:
- A first patent application in 2017, published, and a second application recently filed
- The acceptance of the first scientific paper on the usage of the DSG sensing technology for guidance of robotic surgical platforms at the Hamlyn Symposium on Medical Robotics (June, 2019 in London, United Kingdom). This pre-clinical feasibility study was awarded as Best Paper during this symposium.
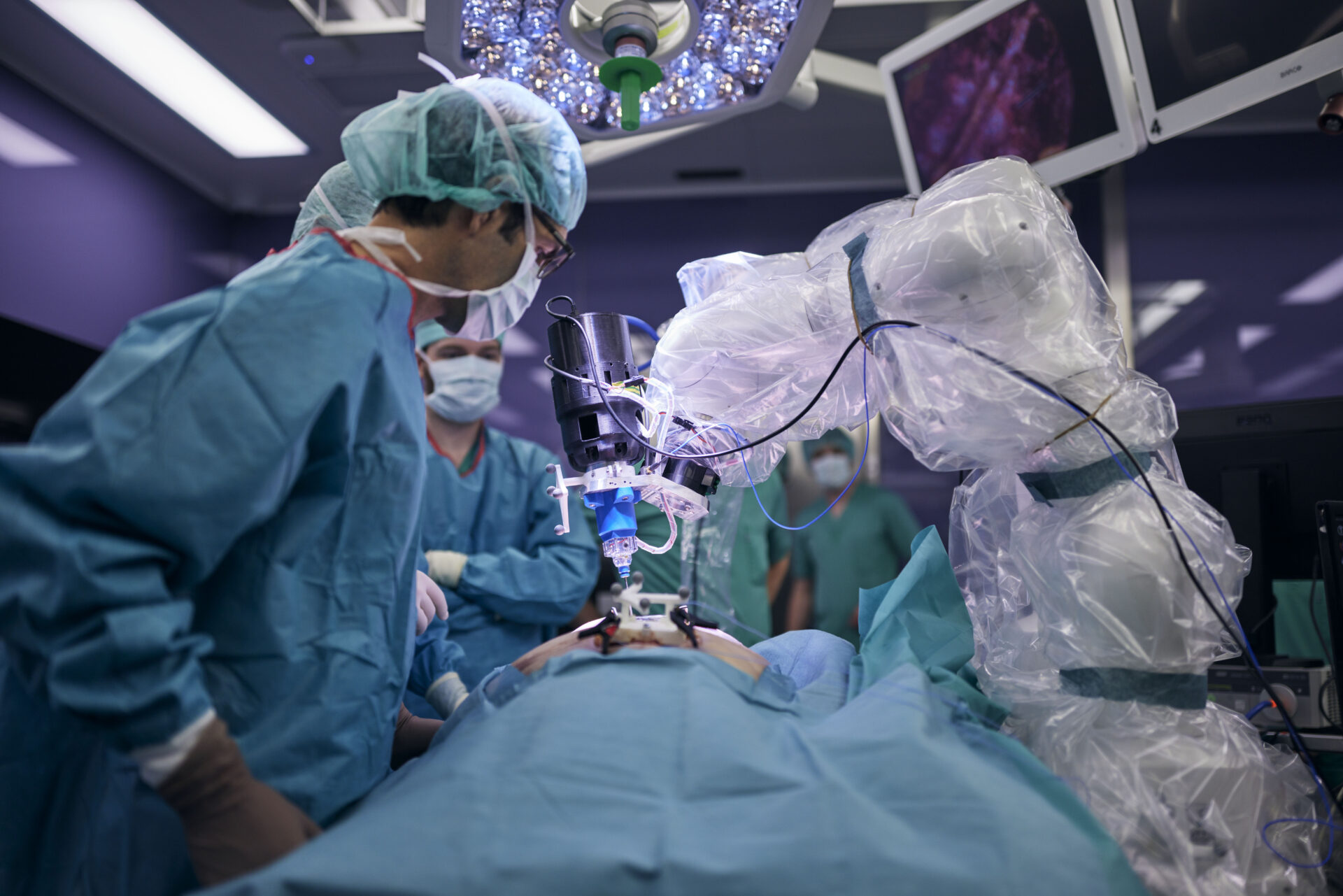
Using an electrical conductivity loop control system for automated breach prevention during robotic powered drilling of bone
Studies 1-4
Current studies conducted in the field of robotic-assisted spinal surgery are focused on using navigation as a tool for optimizing pedicle screw placement and some robotic solutions are already marketed5-7. However, these developments primarily concentrate on outlining and securing the trajectory. The next advancement in robotic-assisted spinal surgery involves optimizing the drilling process itself. The objective was to quantify the performance of tissue electrical conductivity measurement in real time to automatically detect and prevent bone breaches without utilization of imaging technologies in an ex-vivo animal model.
Method
- The setup includes of a container filled with a saline solution, reproducing the electrical conductivity of the cerebrospinal fluid (CSF) and a robot LBR Med 7 of KUKA (7 DOF robot) equipped with a threaded drill bit embedded with the DSG Technology.
- The experiments were conducted on fresh pig lumbar vertebrae, chosen for the similarity of their pedicle morphology, closely mirroring human vertebrae8. The vertebrae were positioned in a clamping vice inside a transparent box and facing a camera, allowing inspection of the canal during the drilling procedure.
- An entry point was made manually, to which the robot was then hand-guided.
- The robot was controlled to apply a constant force along the axis of the drill while maintaining its manually defined orientation.
Results
- 50 drillings completed: a 100% rate of automatic stops before the breach was obtained during the experiment, using the acceptance criteria of ±2 mm between the bone and the spinal canal, according to grade ”A” and ”B” of Gertzbein-Robbins classification9.
- Mean distance to the canal: 0.7mm (-0.9mm/+1.4mm)
Multiple methods were used to verify the results. Firstly, to discard the existence of a breach, a ball-tip feeler palpation was used. Subsequently, a visual inspection of the spinal canal was performed to observe deformations caused by the drill bit tip. Finally, using CT-Scan and the video recorded during the drilling, the absence of false positives was confirmed.
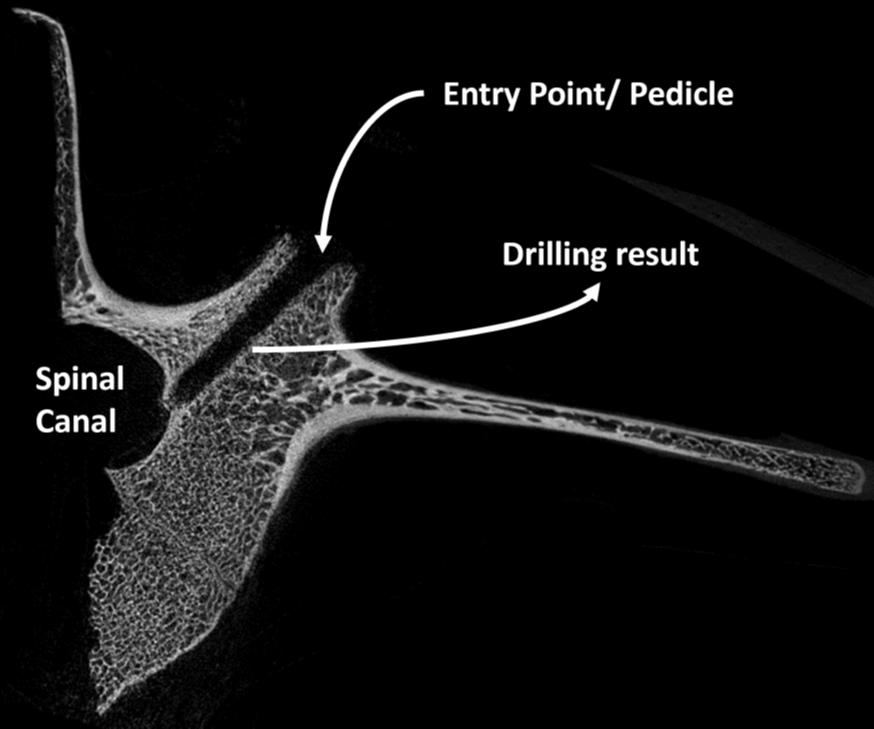
Conclusion
These results demonstrate the robustness and efficacy of tissue electrical conductivity measured in real-time to detect bone boundaries and prevent breaches in a relevant clinical setup. Pig vertebra has proven to be a good alternative to test pedicular trajectories given their similarities with human morphology opening the way for further research.
References
1 – Toward automatic bone breach detection for spine surgery using tissue bio-electrical conductivity sensing. Oral session at Conference on New Technologies for Computer and Robot Assisted Surgery CRAS 2022.
2 – Automatic bone breach detection for spine surgery based on bio-electrical conductivity sensing: Ex-vivo experimental validation. Poster presented at Conference on New Technologies for Computer and Robot Assisted Surgery CRAS 2022.
3 – Force control of the KUKA LBR Med without external force sensor. Poster presented at Conference on New Technologies for Computer and Robot Assisted Surgery CRAS 2022.
4 – Automatic bone breach detection using electrical conductivity during pedicle drilling in spine surgery CRASS. Paper submitted at Conference on New Technologies for Computer and Robot Assisted Surgery CRAS 2023.
5 – M. D’Souza et al., “Robotic-assisted spine surgery: History, efficacy, cost, and future trends,” Robotic surgery, vol. 6,9-23, 2019.
6 – S. H. Farber et al., “Robotics in spine surgery: A technical overview and review of key concepts,” Frontiers in Surgery, vol. 8, 2021.
7 – B. Jiang et al., “New spinal robotic technologies,” Front. Med, vol. 723–729, 2019.
8 – B. I et al., “Comparative anatomical dimensions of the complete human and porcine spine,” European Spine Society, 2010.
9 – R. S. Gertzbein SD, “Accuracy of pedicular screw placement in vivo,” Spine, 1990.